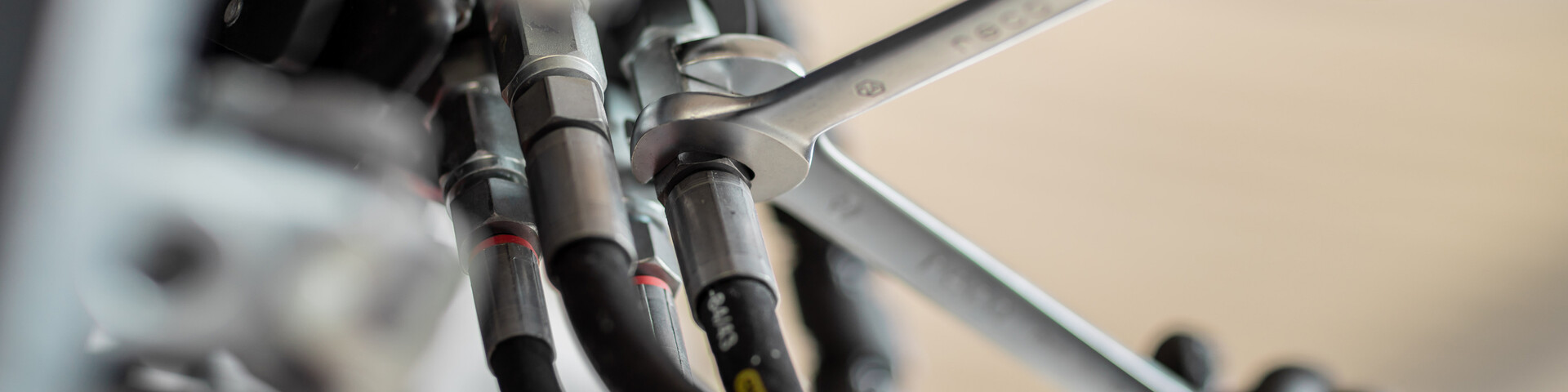
Service & Repair
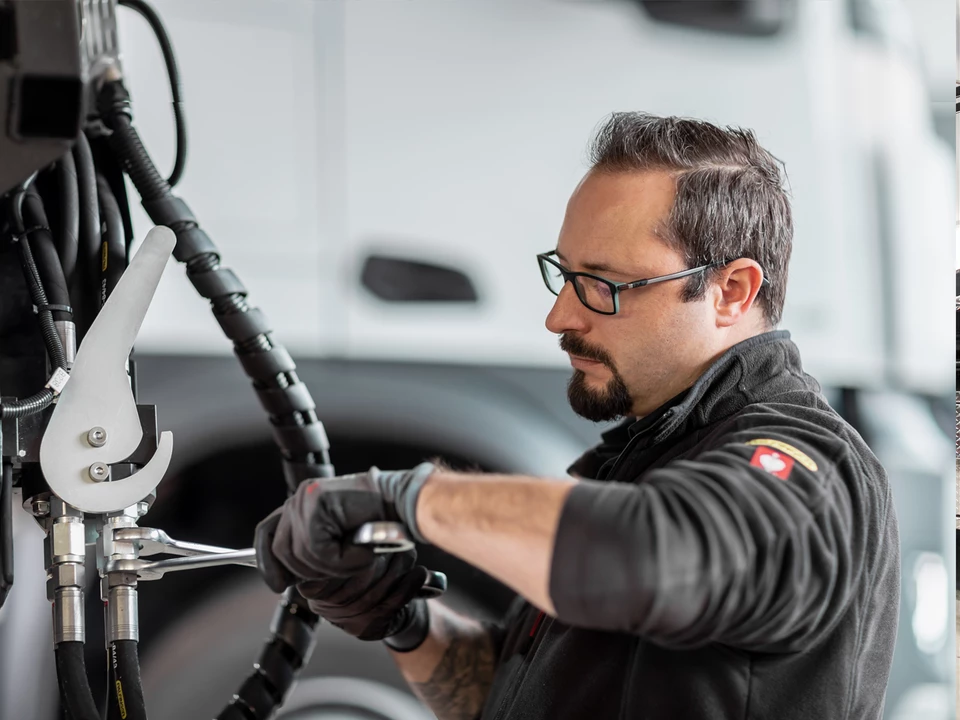

93% OF UNSCHEDULED REPAIRS ARE COMPLETED THE SAME DAY
This outstanding rate isn't just a matter of chance. Our workshops can complete most unscheduled repairs on the same day because our service partners have such a large pool of spare parts. This means that almost all PALFINGER products requiring unscheduled repairs are fully operational again within just a few hours.
THOUSANDS OF SATISFIED CUSTOMERS EVERY DAY
We pull out all the stops to ensure that you can work productively. The feedback that we receive proves that our efforts are paying off. We don’t just rely on hearsay for our feedback – we collect it through detailed surveys conducted by our in-house market research department. According to these surveys, thousands of satisfied customers leave our partners’ workshops every single day.