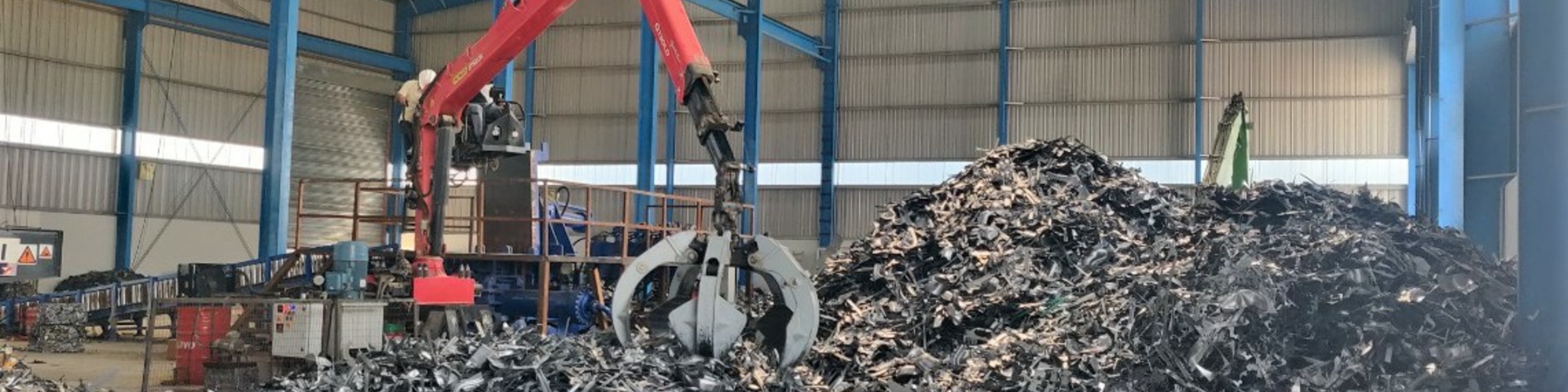
- Home
- News
TATA Steel: Recycling Steel Scrap with PALFINGER
The Company
Tata Steel commissioned its new 0.5 million tonne per annum steel recycling plant at Rohtak, Haryana (North India) in 2020. The unit has been set up in collaboration with Aarti Green Tech, as a ‘Build, Own, Operate’ partner.
The company has also launched two new brands – Tata FerroBaled and Tata FerroShred for the baled and shredded ferrous scrap produced in its new facility. It is the first facility of its kind in India, equipped with modern and mechanized equipment such as shredders, balers and material handlers.
Reduced energy consumption and lowering cost of manufacturing
Metal manufacturing and production of raw materials is extremely energy intensive. Energy costs for metals like aluminium and copper can be reduced by more than 75% by using recycled metal instead of metal ores.
As steel can be recycled again and again without losing its properties, steel scrap is a valuable resource and an important raw material for steel manufacturing. Metal recycling is advantageous to a variety of sectors and businesses. Industries consuming metals in their production frequently generate a significant amount of scrap after producing their goods, so instead of discarding it, recycling the metal scrap can help improve the business economics and contribute to the creation of new jobs.
The TATA STEEL brand is giving a distinct identity to the processed scrap, ensuring a standardized quality product for the customer, and raising the bar of the scrap industry at the same time.
Right from its inception, PALFINGER has been the trusted partner for TATA Steel recycling business with Epsilon Q130LD104 with 350 & 500 liter orange peel grab when they started the business in 2020.
How PALFINGER makes this possible
PALFINGER cranes enable safe feeding of scrap to the Baler with the Epsilon Crane Q130LD014 on a static mount. It is a reliable unit and meets the challenges of the job by maintaining the feed to the production line.
“We have overcome all the challenges faced in our work after incorporating the PALFINGER Epsilon crane. It has made the process of handling scrap much easier, resulting in an increase in production. Running cost also dropped by 50% due to the use of the powerpack as the power source for crane operation. “ ----
One of the key features of PALFINGER cranes appreciated by the customer is the better and clearer views on the top seat to feed scrap to the Baler. Its performance and ergonomics of the operating levers also add to the joy of using our machines.
Contributing to Sustainability
Metal recycling decreases the environmental impact of mining by giving an alternative to unrefined ore. Mining activities disrupt natural ecosystems and pollute the surrounding air, water, and soil, hence recycling metal is critical to reducing the visual pollution connected with metal mining.
Landfills for waste are also a significant source of chemical pollution. Recycling scrap metals minimize the demand for landfills, resulting in cleaner air, water, and land.
About PALFINGER Asia Pacific
For many years PALFINGER (CEO Andreas Klauser) has been one of the world’s leading manufacturers of innovative lifting solutions for use on commercial vehicles and in the maritime field. As a multinational group headquartered in Bergheim, Austria, the PALFINGER Group, which has approx. 12,540 employees, generated total sales of approx. EUR 2.45 billion in 2023.
The Group has production and assembly facilities in Europe, in North and South America, as well as in Asia. Singapore based PALFINGER Asia Pacific was established in 2006 as a regional hub to look after distributors and major customers throughout the region. Today PALFINGER Asia Pacific has 15 dealers across 10 countries in Asia Pacific, with a representative office in Indonesia.
Queries to
PALFINGER Asia Pacific
T +65 6591 9191 | Asia@palfinger.com