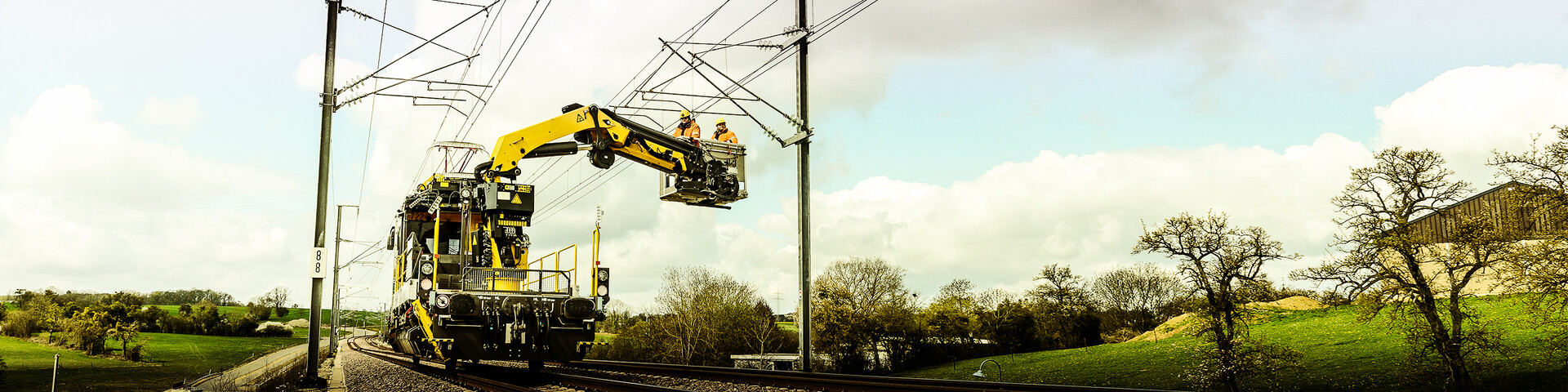
- Home
- Products
- Railway Systems
- Service
A PARTNERSHIP THAT LASTS THE ENTIRE PRODUCT LIFETIME
COMMISSIONING
In order to be able to guarantee optimum performance of PALFINGER products, the following activities are performed by the manufacturer customer service team during commissioning:
- Checking of signal exchanges with the carrier vehicle and between other PALFINGER equipment installed on the same vehicle.
- Adjustment of safety-relevant systems, such as height limitation and opposite track blocking
- TÜV approval and handover to customer
- Operator training
Commissioning by the manufacturer guarantees that devices are operated safely and in the most effective way.
Optimised lifting capacity/outreach of the machine in terms of stability according to customer specifications.
Consideration of the following criteria:
- Slewing angle
- Track cant
- Vehicle at standstill or creep speed
- Position of support legs
- Vehicle frame deflection
- Detachable counterweight
- If applicable - further PALFINGER units on the same vehicle
- Depending on the vehicle concept - further relevant parameters
Training
In a competitive global environment, specialist expertise is a key factor for success. The PALFINGER Railway training team puts its knowledge at your fingertips. Increased efficiency and safety through continuous further training.
We combine products, activities and services to share knowledge:
- Clear training methods and materials
- Skilled trainers and contacts
- Modern, practical training systems in company-owned training centre
- Progressive course programme to build trainee knowledge
Greater knowledge, more benefits and better application of knowledge for:
- Operators and users
- Internal and external service technicians
- Operator service staff
- Maintenance staff
TO TRAIN
As a leading global specialist, PALFINGER possesses wide-ranging technological expertise.
Trainees receive individual training in small groups to learn the basics, gain a fundamental understanding of key principles and develop expert knowledge.
Training is provided at the company-owned training centre in Salzburg or at the customer’s own site.
TO UNDERSTAND
The modular training programme is designed to develop technical understanding and give participants the skills they need to solve problems, whether the participant is a newly recruit to be qualified or an established, experienced technician.
Practical learning exercises effectively convey and allow participants to understand the learning content.
- e-learning with online access to PALFINGER education modules
TO APPLY
By accompanying the customer on site and collaborating closely, the operators learn to unlock the full potential of PALFINGER devices.
- The knowledge acquired in the theoretical element of the course is put into practice here
- Support during use; identification of issues arising during everyday use, as well as resolutions for these issues
- Product and customer-specific training for workshop staff
Service
PALFINGER Railway supports servicing and maintenance work, no matter whether it is performed by the PALFINGER customer service team or the customer’s own technicians. Planned measures are better than unplanned breakdowns.
- Regular servicing and inspections extend the service life of the device and guarantee safety for the user.
- Early identification and repair of damage, and the performance of preventive maintenance, increase device availability.
- In order to ensure the continuity of maintenance work, PALFINGER Railway offers a range of optional service contract programmes.
- If a backlog of repairs or servicing work arises for a device, PALFINGER will be happy to carry out this work following a prior assessment. Request a quotation from PALFINGER!
TELEPHONE SUPPORT
An experienced team is on hand to provide advice and assistance. Whether you have technical questions, or need to request spare parts or documentation, the PALFINGER Railway team will be happy to help.
REPAIRS
If a product becomes damaged over time, you can rely on the extensive PALFINGER Railway service network! Our employees will provide you with fast, competent support on site:
- Our team benefits from extensive training, has access to all data and uses original spare parts, all of which guarantee skilled repairs.
- Any design improvements are incorporated into original documentation, such as the electronics and hydraulics plans, as well as the spare parts catalogue, as necessary.
- The manufacturer’s technicians are in the best position to carry out professional repairs.
MODIFICATIONS
If our customers’ requirements change, if adjustments need to be made to accommodate local circumstances or if our customers simply want to improve efficiency, PALFINGER RAILWAY is pleased to offer modification services.
- Requirements for vehicles and devices that are used for maintenance and repairs often change over time. Various attachments are available, and changing the field of application or specialising in certain applications can facilitate increased efficiency by making improvements to the product.
- The manufacturer’s competent staff and the availability of a complete database guarantee high-quality, safe modifications to the device. A device can be adapted to suit virtually any customer requirements.
Adapted designs increase versatility and maximise efficiency.
RENEWAL
Retaining old devices is advantageous in a number of situations. Firstly, the vehicle‘s licence is retained, and secondly, operators do not need to be retrained. The PALFINGER modernisation programme doubles the product lifecycle and has many other advantages, including:
- Extends the product’s service life – new purchase not necessary
- Due to little kilometric performance, the service life of the carrier vehicle is limited by the superstructure, which could almost be doubled by a modernisation.
- Replacement of faulty parts reduces downtime and increases availability
- Possibility to improve performance by making technical enhancements
- Adaptation based on customer requirements
- Improved appearance
- Wear parts renewal
- Obsolet components are replaced by the equivalent new versions
Example of a renewal programme
SPARE PARTS
The only way to guarantee the safe and long-term use of a device is to exclusively use original spare parts. Technicians from the PALFINGER Railway customer service team and certified service partners have access to the extensive PALFINGER spare parts depot.
- PALFINGER Railway products have a very long service life. Service lives of 20 years or more are not uncommon. A specialist team manages the spare parts supply for all devices on the market – for up to 10 years after the model has been discontinued, and often longer.
- Direct contact with customers and vehicle manufacturers ensures that spare parts requests are handled quickly, without excessive administrative procedures.
Contact Austria | Italy | Switzerland
Manuela Toskic
T +43 / 6216 7660 - 85621